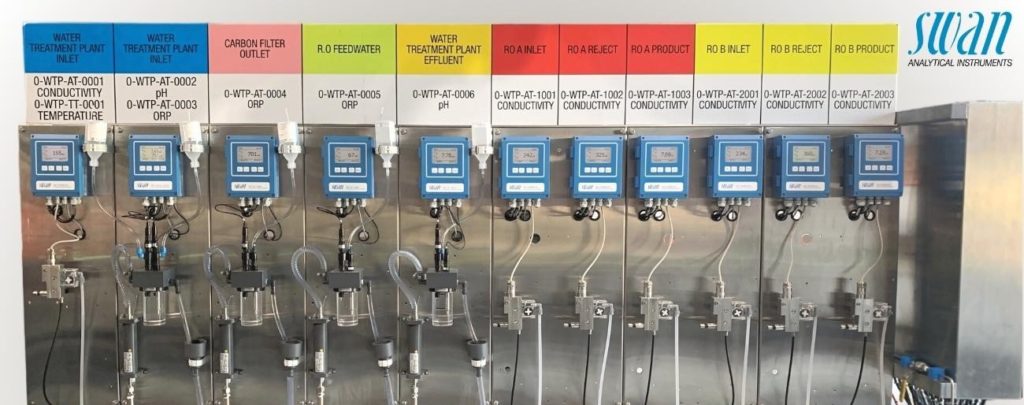
In 2023, a prominent power station in Far North Queensland (FNQ) needed to upgrade its water analytical equipment to improve reliability, reduce maintenance costs and ensure the water treatment plant maintained efficiency.
Swan Analytical Instruments was chosen for the project due to their reputation for accurate and reliable equipment, as well as the reduced maintenance requirements, ergonomics, and easy-to-use design. The installation of a robust wet rack and water monitors assures the continued efficiency, safety, and reliability of water treatment operations at the power station.
Background
A power plant located in northern Queensland supplies electricity to approximately 240,000 Australian households. The energy company that owns the power station is a loyal customer of Swan Analytical due to the reliability of Swan instruments. The large, public company exclusively uses Swan analysers at all their Australian sites. One of these sites (in NSW) includes full SWAS for four units, installed almost 15 years ago and still fully supported by Swan Analytical Instruments Australia Pacific.
A wet rack with water analysers monitors the quality of water used in the power plant in their boilers, thereby ensuring a safe and efficient operation.
The Problem
Previously, the water treatment plant had used analysers from other well-known brands. However, after less than ten years of use, they all had to be removed because the power station reported they were unreliable, unserviceable, and lacking in support and availability of spare parts. This caused the water treatment plant to suffer many failures during its operation.
Water analysers are used to monitor the quality of water feeding and being produced by the reverse osmosis (RO) / electrodeionisation (EDI) water treatment plant. The analysers detect impurities in the feedwater, which could cause scaling or degradation in the RO/EDI plant, thereby reducing its efficiency. The analysers also monitor the quality of the output water to ensure that the water treatment plant operates correctly.
The Solution
A wet rack with water analysers was installed to ensure the quality of water feeding and being produced by the reverse osmosis / EDI water treatment plant. The wet rack is a stainless steel structure that houses the analysers and allows water samples to flow through them for analysis. Samples from the feed water, reverse osmosis plant and the EDI units are monitored to ensure that each unit operates correctly and produces water to specification.
The installation was completed in May 2023, within just six weeks of approval being granted. Online analysers were set up to measure pH, ORP, and conductivity in the water. In this project, the Swan AMI pH/Redox Monitor, Swan AMI pH mV/mV Monitor, and Swan AMI Powercon Specific monitor were used.
The FNQ SWAS wet rack with Swan analysers is reliable and easy to maintain. Quality monitoring instrumentation, such as Swan Analytical Instruments, dramatically prolongs the life of boilers and steam systems. With this new setup in place, the power station operations will be efficient and reliable going into the future.
Swan Analytical Instruments were chosen for this project because of their demonstrated dependability, minimal need for maintenance, and easy-to-use interface. Furthermore, they are backed up by the highly skilled team at Swan Analytical Australia.
Challenges Faced
The installation of the wet rack posed several challenges, including the need for a stainless steel structure that could withstand harsh environmental conditions. The placement of the wet rack was also challenging, as it needed to be located in an area that was easily accessible but also out of the way.
In partnership with Queensland-based company Hamilton, Swan Analytical found solutions to these challenges and delivered a durable and reliable water analysis system.
Conclusion
The installation of Swan Analytical Instruments water monitoring systems in a large Queensland power plant has enabled the plant to improve its operational efficiencies, reduce maintenance costs and maintain reliable operations going forward.
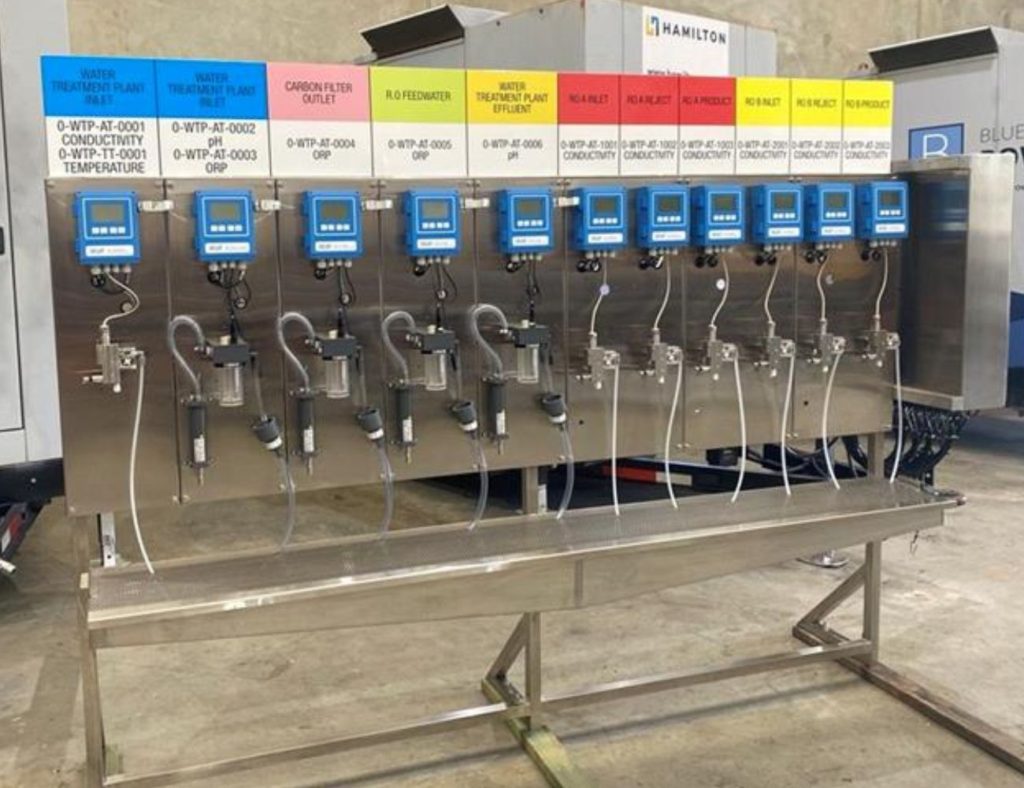
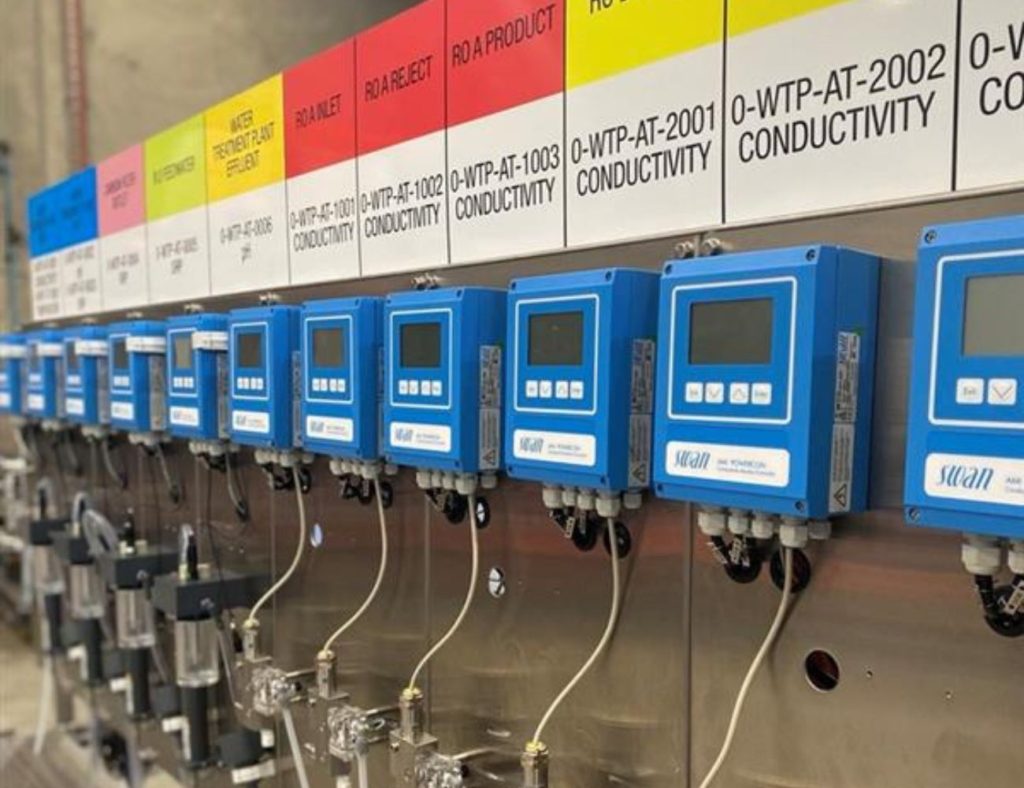
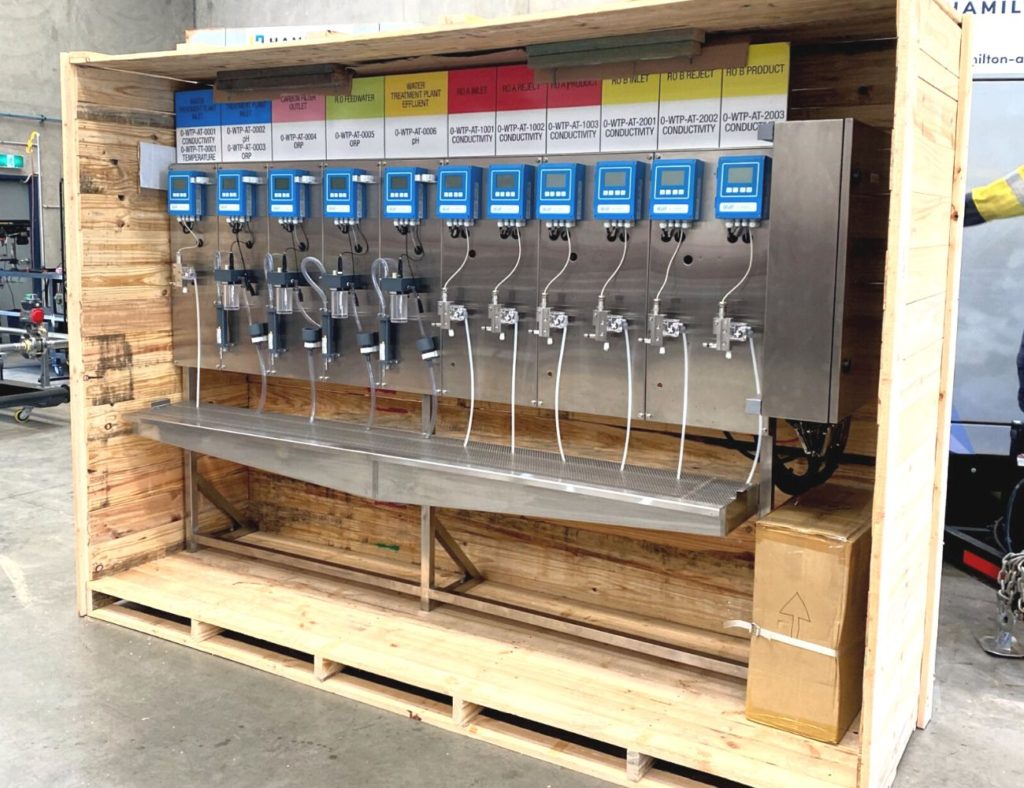
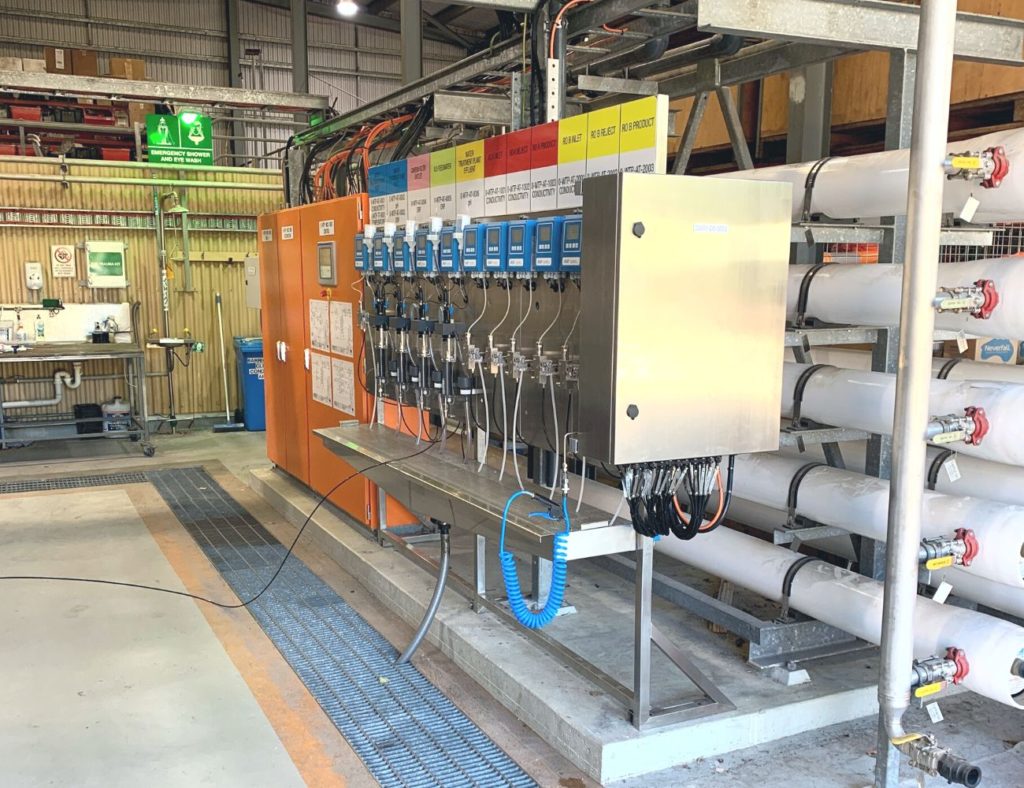
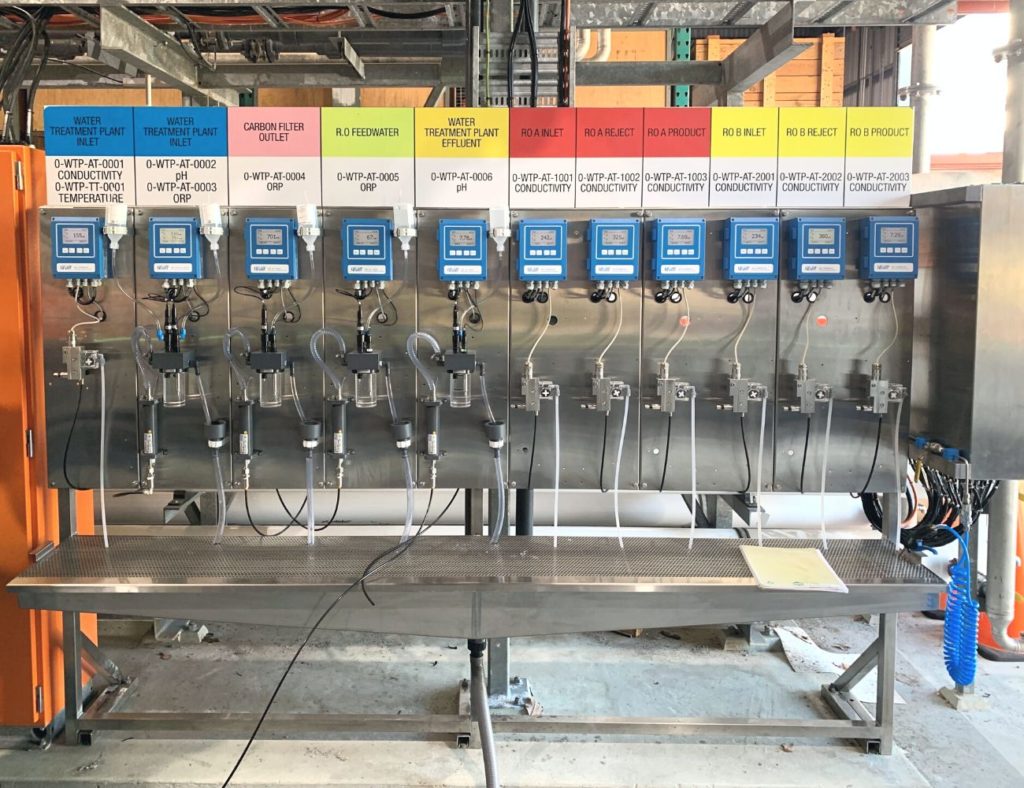